Health & Safety News to Live By – Q321
Remembering 9/11
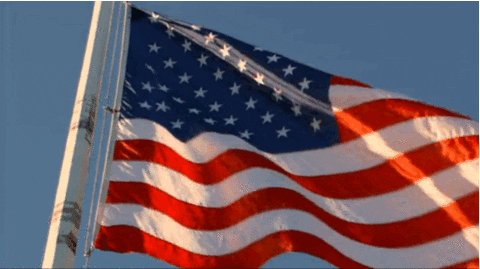
This year, our country recognized the 20-year anniversary of the September 11, 2001 terrorist attacks on our home soil. While this remembrance event occurred over a weekend, a few select project teams were working at various client sites. One project, in particular, found a special way to honor those lives lost and the actions of the countless first responders reacting to the tragedy. |
The scope of the active project included fire hydrant replacement in excavations requiring standby rescue teams. The outfit selected to provide these resources employs many New York City firefighters. Understanding the gravity of the situation, the entire workforce on this project voluntarily stopped work to provide a moment of silence in remembrance. One subcontractor, in particular, provided the confined space rescue crew with gift bags as a sign of both respect and honor for their role in responding to the 9/11 catastrophe. CD & Associates is so incredibly proud of the actions taken by our workforce and commend their behavior. We would also like to extend our continued thoughts to those both directly and indirectly affected by the events of 9/11. We stand with you. |
Block Kids is Back!
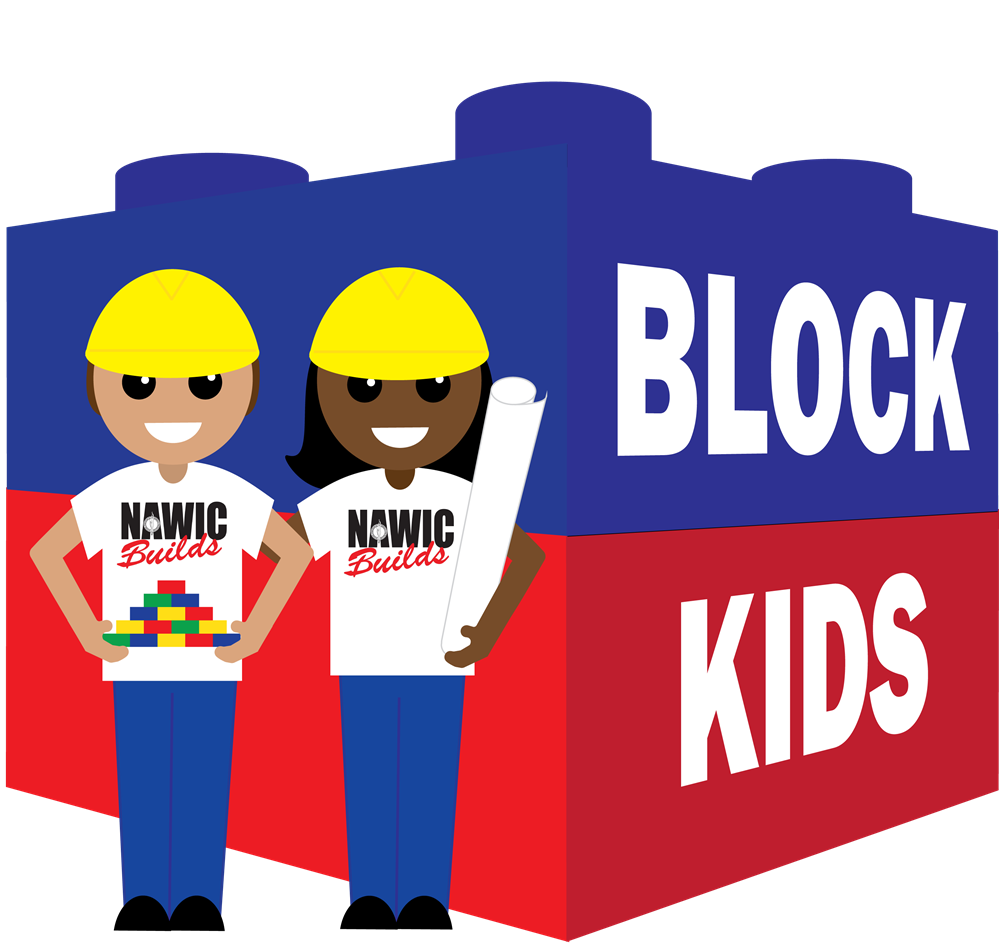
The Block Kids Building program is a national and award-winning program sponsored by various National Association of Women in Construction (NAWIC) Chapters across the US and Canada. Locally, this event is sponsored by the NAWIC Philadelphia’s Education Foundation (NEF). This event challenges students in first through sixth grade to use their imagination and innovation to create a structure or project using self-interlocking blocks and additional items- string, foil, a small rock, and poster board. The projects are then presented to a team of judges comprised of professionals in the industry. The goal of the program is to introduce our youth to the excitement and future opportunities in the construction industry. This year’s event is scheduled for Saturday, November 6, 2021 at the Sheet Metal Workers Local 19 Hall in Philadelphia.
We are proud to sponsor this great event again!
To register participants, please visit the enrollment page.
Did we convince you to sponsor? Please visit the sponsorship page.
Our Commitment
The Q2 Whole Body Health & Safety Bingo Challenge was a success! Our employees had a great time checking off activities on our bingo card encouraging movement and time outdoors. Check out some of the pics! Categories included here are kayaking, chalking a positive message, star gazing, playing a board game outdoors, visiting a state park, camping, and playing an outdoor sport.
Our Q3 Challenge is a Step Challenge! Participants have been assigned to teams for this 3-week activity. The team with the highest average steps will be treated to a special lunch, while individuals who average over 10,000 steps per day will be rewarded with a gift card. We are so excited to offer these events encouraging healthy habits, but are also thrilled at the teambuilding and morale boosting results!
Safety Success: Electrical Upgrades
Our project team was recently announced as the winner of a client safety award for an electrical upgrades project. The existing facility condition included a 480V electrical system with an indoor substation as well as 6 motor control centers (MCCs). The substation is equipped with antiquated circuit breakers, auto transfer system, and high resistance ground system. The substation’s 13.8KV – 480V transformers were determined to be in good condition upon inspection. The existing configuration and condition of the circuit breakers and auto transfer system, however, left the chiller building susceptible to unplanned outages. The existing equipment provided limited diagnostic capabilities, potentially leading to lengthy outages in the case of equipment failure. Additionally, the MCCs were of similar vintage as the substation and had limited spare parts availability, creating a risk of a lengthy outage in the case of a failure. The configuration of this limits the serviceability of the ancillary equipment supporting chiller operation (pumps, compressors, etc.). The systems were also electrically interconnected which would require that multiple systems (chillers, etc.) must be placed out of service to perform maintenance or repairs on an individual piece of equipment.
In an effort to correct these conditions, our project refurbished existing 480V substation with all new circuit breakers, metering system, auto transfer system/controller, and a high performance ground system. The refurbished upgrades will allow for a greater reliability, easier load transferring, and provide additional information for maintenance and repairs. Along with the substation refurbishment, the project also performed electrical upgrades to replace five (5) antiquated MCC’s with two (2) reliable MCC’s and three (3) MDP’s. All building loads were then disbursed more evenly between the MCCs and MDPs to allow for easier shutdowns in the future.
Our keys to success:
Design: Re-use of existing conduit and pathways to minimize field tasks; equipment fabricated off-site.
Risk Management: Engaged SME contractor for QC checks on temporary electrical plan that backfed specific loads to ensure no loss of critical utility support during shutdown.
Procurement: Selected contractors based on proven field execution, safety record, and prefabrication capabilities. Safety expectations included in contracts.
Pre-Planning: Multiple, compliant scaffold systems erect for safer access to elevated work locations; extensive LOTO procedures employed.
Innovation: Installed material transport platform to second floor which eliminated multiple crane lifts and allowed for entire pre-fabricated MCCs to be delivered and installed at one time reducing work required on-site.
Health & Safety Solutions
Our Health & Safety Solutions division is currently partnered with local steel fabricator and erector, Berlin Steel, on a 14-story integrated office, lab, retail, and higher education development project in Philadelphia. CDA’s own Joe Fitzpatrick, a former ironworker himself, has been leading the charge with boots-on-the-ground EHS oversight for the steel workforce comprised of roughly 50 workers daily. This entails reviewing project safety documentation, providing training and orientation, maintaining personal protective equipment inventory, overseeing all aspects of high-risk work including elevated work, crane lifts with the two tower cranes, and hot work activities, conducting pre-planning meetings and toolbox talks, attending coordination meetings, completing project audits, and equipment inspections. Check out some of the pics below and remember to contact CDA for any consulting, auditing, and training needs!

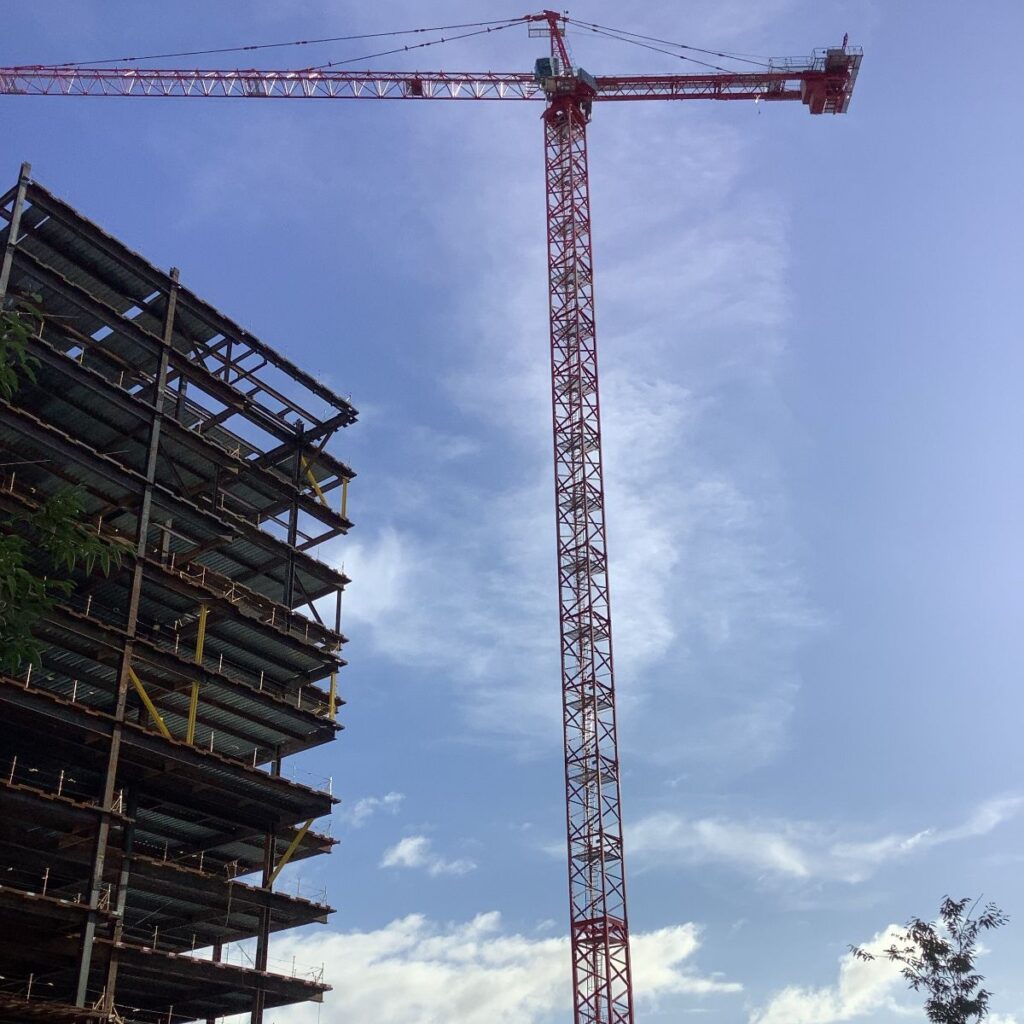